结合该工程实际,沥青路面施工流程:施工准备→混合料制备与运输→摊铺参数确定→摊铺施工→路面压实→路面接缝处理。
2.1 施工准备
路面施工前,为满足路面结构压实度和平整度要求,施工单位对基层压实度恶化平整度进行检查处理,对凹凸部位进行铲除、补平处理,修整部位采用压路机碾压至平整。待基层检查合格 6 h 内喷洒沥青透层,透层油采用乳化沥青 PC-2,喷洒面积根据试洒确定(1.5 L/m²),沥青透层厚度大于等于 5 mm。沥青透层喷洒后,及时养护处理,为路面施工创造良好条件[1]。
2.2 混合料制备与运输
混合料制备质量是影响沥青路面施工质量的重要因素,为防止因沥青混合料制备质量不满足工程施工质量要求,改工程严控混合料材料质量和混合料出厂质量,并加强混合料运输管理。
混合料材料管理中,沥青基质针入度(25 ℃,100 g,5 s)控制 6~8 mm,延度(5 cm/min,10 ℃)大于等于20 cm,软化点大于等于 46 ℃,质量损失小于等于0.6%,闪点大于等于 250 ℃。级配碎石选用石灰岩碎石,压碎值为 17.6%,符合技术标准要求[2]。
混合料配合比根据试验确定,水温定性合格,实验确定最佳油石比为 4.5%(表 1),残留稳定度大于等于 85%。混合料拌合中严格按配合比设计投料,确保施工配合比与设计配合比相符[3]。
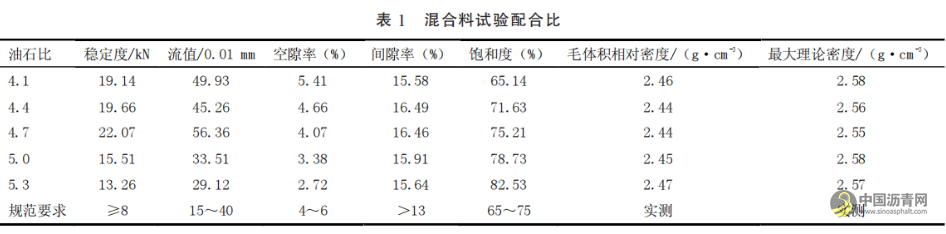
混合料拌合出厂质量控制时,采用马歇尔实验和旋转压实实验方法检验混合料质量,混合料稳定度大于等于 8.0 kN,流值控制在 2~4 mm,空隙率控制4.0%~6.0%,沥青饱和度控制在 60%~70%,骨架间隙率大于等于 12%。初始压实度小于等于 89%,设计压实度为 96%,最大压实次数时压实度小于等于 98%。混合料拌合完成后采用专用运输车运输。运料车每次运输前后均清理车厢,防止残留集料影响混合料性能。为防止混合料与车厢黏连,运料车清理后涂刷1 层隔离剂。装料时,运料车前后移动 3 次,按“前—后—中”方式循环装料,避免出现车辆中间高于前部、后部情况。防止混合料滚落、离析。混合料运输到施工现场后,由质监人员检查混合料质量,防止劣质材料进入施工现场,经检查合格后方可投入使用[4]。
2.3 摊铺参数确定
为合理确定大面积摊铺施工参数,施工单位划定100 m 作为试验段,根据试验段施工参数确定大面积摊铺施工参数[5]。
根据试验结果,摊铺厚度按混合料中集料最大粒径 2 倍作为沥青摊铺厚度(48~52 mm),混合料松铺系数为 1.15~1.20。单次摊铺宽度 7.5 m,摊铺接缝重叠宽度大于等于 50 mm,分层摊铺上下层接缝错位宽度大于等于 200 mm。前后摊铺机距离大于等于 10 m。摊铺机械设备选择时,考虑到该工程施工质量、施工进度等要求,确定选用德国 Vogele 1800-3 型履带式摊铺机,该摊铺机摊铺宽度为 3.0~7.5 m,最大摊铺厚度为 300 mm,前进速度为 0~20 m/min,回转半径5.8 m。并配备了高精度螺旋式送料器,可实现均匀、连续送料,摊铺精度为±2 mm,能够有效控制摊铺精度。摊铺温度控制时,在确保混合料出料温度满足技术要求的前提下,混合料运输到场后由专人检测温度,确保混合料卸料温度控制在 155~165 ℃范围内,防止混合料冷却凝固或老化。摊铺施工中,借助摊铺机自带红外热像仪间隔 5 min 扫描测量混合料温度,配合人工检测温度,可实现全幅范围内混合料温度变化监测。
2.4 摊铺施工
摊铺施工是路面施工的重点环节,为确保摊铺质量,该工程采取摊铺技术措施包括:①摊铺机提前 30~60 min 预热熨平板至 120~130 ℃,防止熨平板与混合料温差过大而造成黏连问题;②摊铺机储料斗料位高度保持在 60%~80%,结合摊铺机料位传感器监测数据和摊铺速度自动控制出料速度,防止因料斗供料不足造成局部缺料、厚度不均问题;③下面层摊铺前设置钢丝绳引导摊铺机走向,道路摊铺宽幅两侧设置高程、水平测量网,以此控制摊铺路幅摊铺线形和摊铺厚度,防止发生较大挠度或变形问题。下面层施工中加强监测高程、水平测量网支撑有无松动情况,一旦发现支撑点松动、倾斜及时恢复;④摊铺机行进速度为 3.0~5.0 m/min,严格控制摊铺机行进速度,防止因加速和急停造成路面摊铺厚度不均问题;⑤摊铺机梯度前进,相邻摊铺机沿路线放线距离为 5.0~6.0 m。摊铺搭接宽度为 200 mm,确保路面摊铺搭接顺直,避免混合料推移问题[6]。
摊铺施工时,摊铺机需保持均匀速度行驶,避免急刹、急停、突然加速及急转弯等操作,以免因操作不当导致路面出现车辙。
施工过程中,施工单位应加强摊铺厚度的检测,尤其是转弯及路肩等重点部位,若发现厚度不足或超厚,需及时通过人工处理,确保改性沥青路面厚度均匀,符合设计要求。
混合料摊铺时,除非出现特殊情况(如下雨、机械故障、断料或安全事故),不得中断施工。如因客观原因需暂停,应缓慢停下摊铺机,避免急停引发混合料离析或下承层破坏。中断时间小于等于 30 min,经检测混合料合格后可继续施工;中断时间大于 30 min时,需重新加热熨平板并确认混合料温度合格后再恢复施工,不符合要求的混合料应作为废料处理[7]。
2.5 路面压实
施工过程中,严格按照初压、复压和终压 3 个阶段进行压实施工。碾压操作自低向高进行,压路机轮迹与道路中线保持平行,为消除轮迹,轮迹需重叠 80~100 mm。由于混合料摊铺后降温较快,为加快封闭路面,施工单位使用 12 t 钢轮压路机压实施工,复压采用 18 t 双钢轮振动压路机与 28 t 轮胎压路机联合碾压,终压采用 18 t 双钢轮压路机压实施工消除轮迹。
2.5.1 初压
混合料摊铺后,及时进行初压施工,初压施工采用德国 CC422D 型 12 t 双钢轮振动压路机碾压施工,压路机碾压宽度为 2.13 m,可实现振动频率与振幅无级调节,可满足该工程沥青混合料碾压施工要求。初压施工中,由于混合料摊铺后热量易散失,导致混合料温度下降速度加快,压路机紧跟摊铺机碾压施工,初压温度控制在 145~150 ℃,初压速度为 2.0~2.5 m/min,振动碾压 2 遍,振动频率为 50~55 Hz,振幅为 0.4~0.6 mm。使沥青混合料摊铺后初步密实、及时封闭,提高混合料稳定性,防止出现收缩、裂缝等质量问题。路面初压后,检查路面平整度与横坡度,发现路面局部凹陷或凸出时人工整平处理。初压施工中,施工单位安排专人记录初压遍数、行进速度、轮迹重叠宽度等数据,结合初压施工中出现的问题及时调整碾压方案,防止出现欠压、过压等质量缺陷。为确保初压施工中均匀性,施工单位采用分幅碾压方式,2 台压路机重叠宽度大于等于 300 mm (图1),便于消除轮迹。
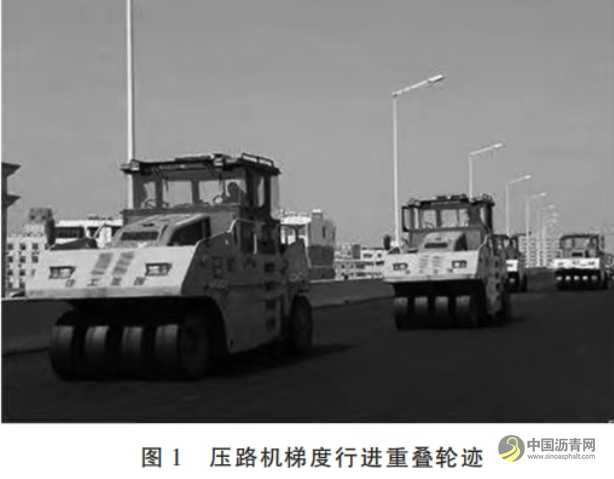
2.5.2 复压施工
复压施工中,采用 18 t 双钢轮振动压路机与 28 t轮胎压路机联合碾压,利用低频高幅振动组合实现混合料深层压实,增强路面密实度和强度。复压时,混合料温度控制在 110~125 ℃。双钢轮振动压路机率先碾压,振动频率为 30~35 Hz,振幅 1.0~1.2 mm,碾压速度为3~4 km/h,碾压 4~5 遍,直至表面无明显轮迹。施工过程中,通过密度仪动态监测路面压实度,每碾压 2 遍后结合钻芯测试空隙率进行质量评估。当连续 2 次测得压实度变化小于 0.5%时,停止复压。试验段结果表明,复压遍数控制在 3~5 遍(表 2),压实度需达 97%以上。
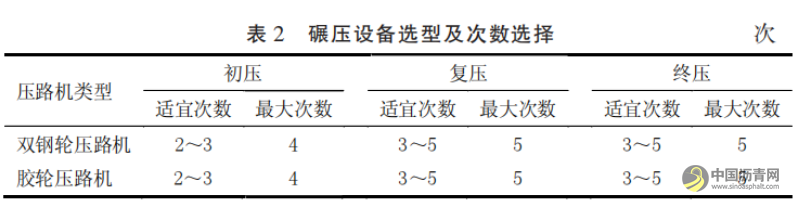
待双钢轮压路机碾压后,胶轮压路机紧随作业,胎压为 0.8~1.0 MPa,碾压速度与双钢轮压路机一致,碾压 4~5 遍。轮胎碾压通过嵌锁和挤压作用,增强混合料骨架摩擦力,提高路面抗变形能力。
2.5.3 终压施工
终压阶段使用 20 t 钢轮压路机碾压施工,碾压速度控制在 50~60 m/min,碾压温度为 80~100 ℃,碾压2 遍直至表面无轮迹。
2.6 接缝处理
沥青路面接缝处理中,为提高接缝质量,本工程采用热缝处理方式。纵缝处理时,摊铺机以梯度方式施工,预留 200 mm宽路面暂不碾压,作为道路路拱。上下层纵缝采用150 mm 错缝搭接处理。施工前在接缝处涂刷黏层油,并利用摊铺机预热接缝部位,随后摊铺接缝区域以增强黏结性能。摊铺机应在已完成施工的路段上行驶,接缝处混合料宽度 200 mm,经过压路机碾压压实至平整,与整体路面无缝衔接。
横缝处理时,结合沥青混凝土路面黏性强的特点,采用下面层斜缝搭接和上面层垂直平缝搭接处理。施工开始时,在摊铺机起点位置放置 100 mm×100 mm木方作为基准,施工机械从木方起点处作业。施工完成后,人工切割接缝位置路面至下面层,填入混合料并压实。随后使用双钢轮压路机对接缝进行横向碾压,确保接缝与新铺路面平整。接缝处理完成后,通过钢尺检测平整度,确保接缝部位充分压实且平整。